(视频)
5月21日,随着Z2-3边跨合龙节段的滚装发运,标志着由央企中铁宝桥参建的常泰长江大桥主体结构全部发运完成。
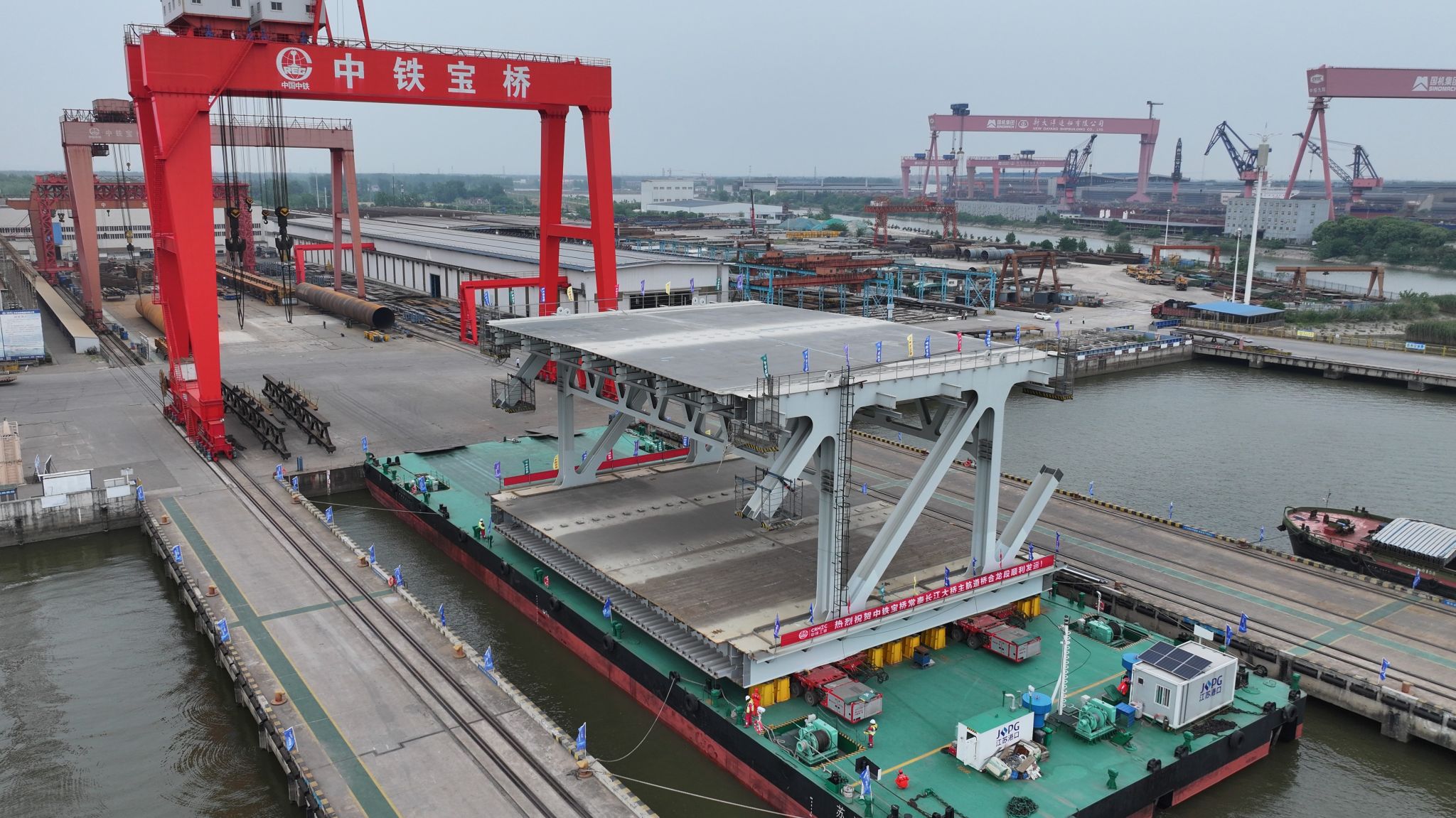
▲大节段发运现场
常泰长江大桥主航道桥钢桁梁为箱、板、桁组合桁架大节段形式,桁宽35米,桁高15.5米,标准节段长度28米,最大单重1866吨,中铁宝桥厂内共制造46个节段,分15轮总拼,Z2-3节段作为边跨合龙节段,是最后一个大节段,节段长28.7m,宽39m,高17.4m,总重约1344.5吨。
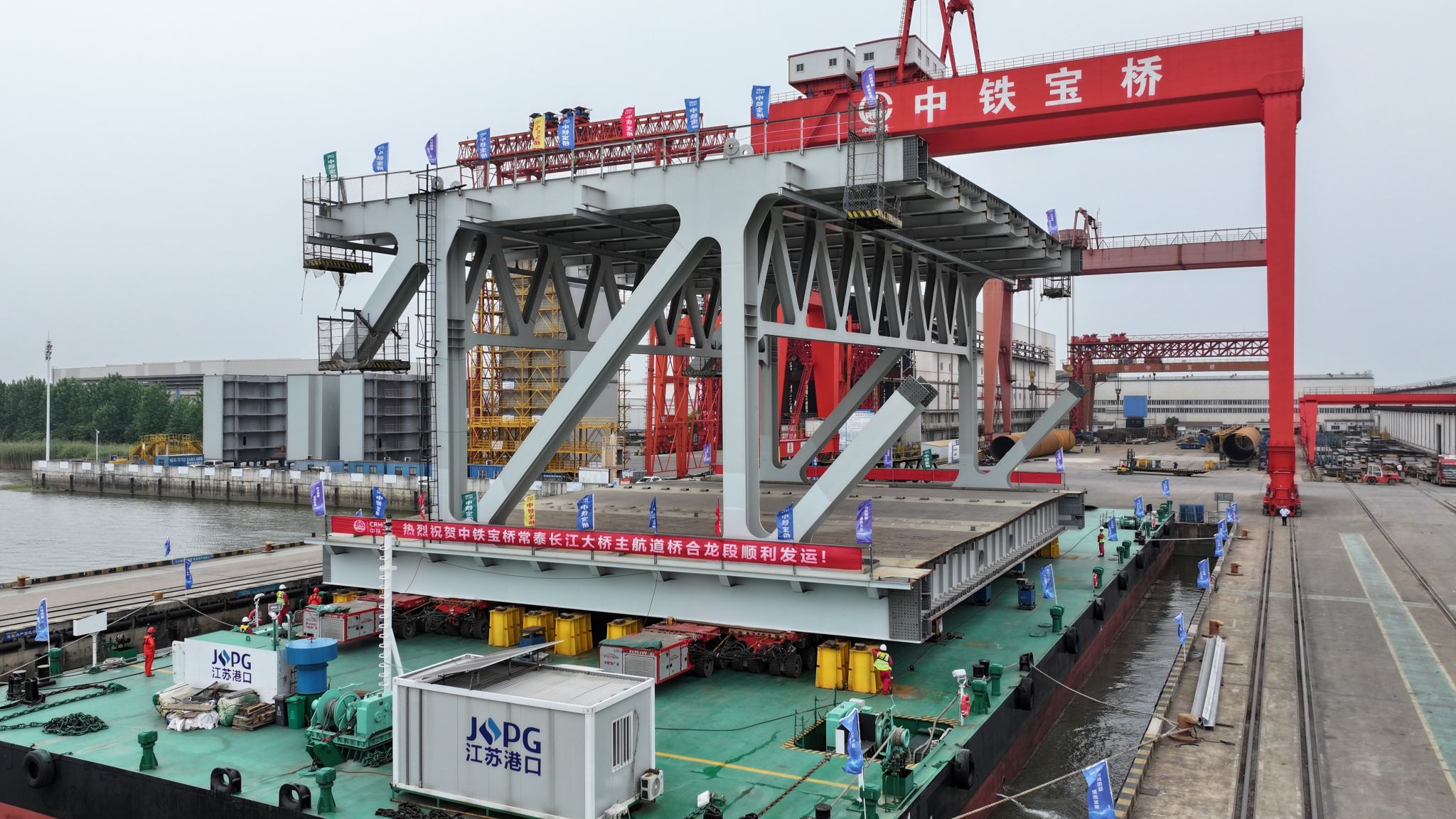
▲边跨合龙节段
常泰长江大桥是长江上首座集高速公路、城际铁路、普通公路“三位一体”的跨江大桥。大桥全长10.03公里,位于泰州大桥与江阴大桥之间,主航道桥采用主跨1208米斜拉桥,是中铁宝桥历史上单体合同—钢结构重量、金额最大的项目,为目前在建世界最大跨度公铁两用斜拉桥,建成后将实现“四个国际首创”,刷新“六个桥梁之最”,对推进“一带一路”交汇点建设、更好地服务长三角一体化发展和长江经济带发展战略,完善区域路网布局,促进扬子江城市群协调发展等具有重要意义。中铁宝桥参建的常泰长江大桥CT-A5标包括主航道桥南北钢塔及主塔索塔锚固系统、主航道桥跨中以北钢桁梁大节段、天星洲专用航道桥钢桁梁等钢结构加工、制造、运输及桥位现场连接,总工程量约13.2万吨。
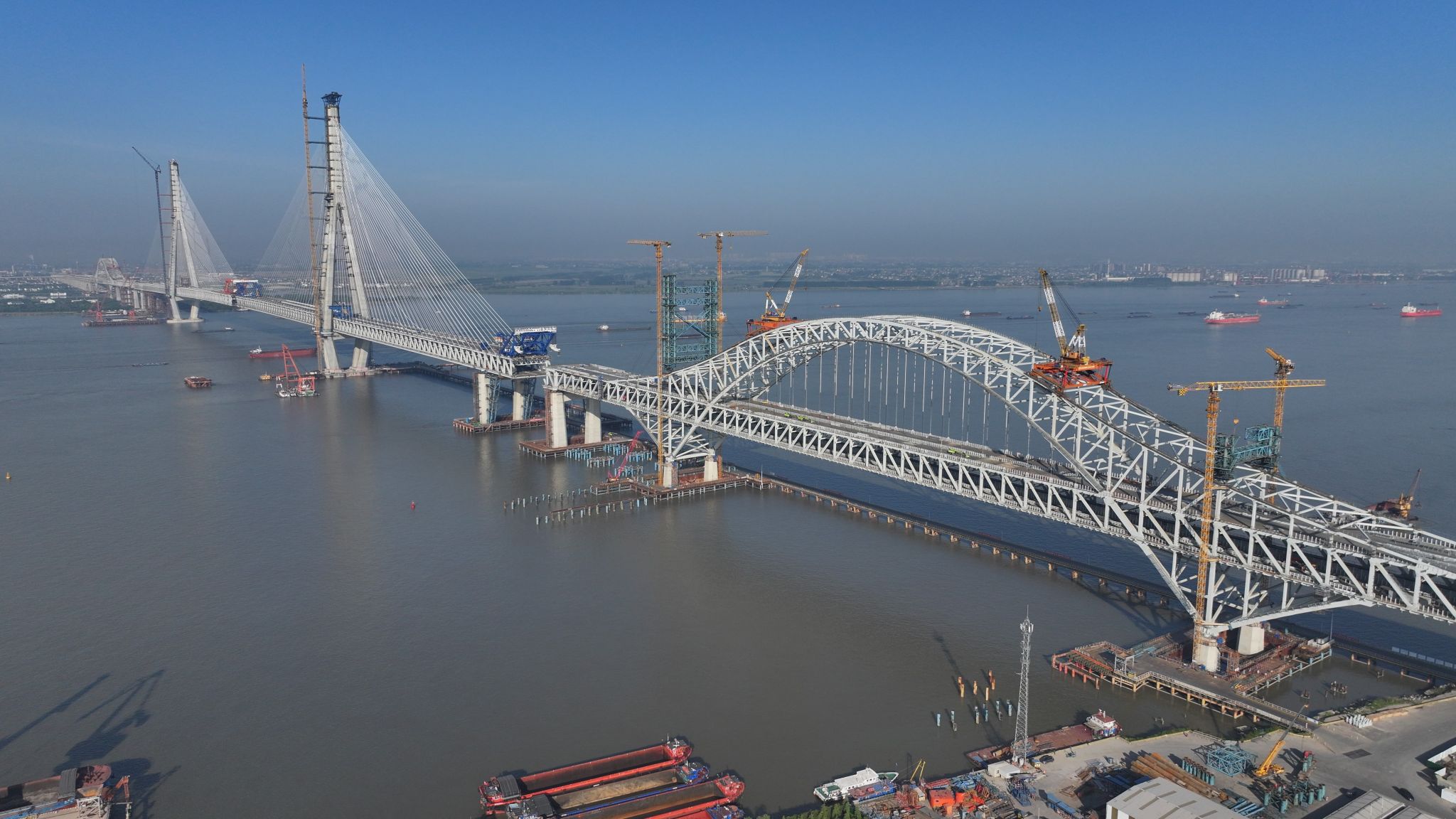
▲常泰长江大桥
依托常泰长江大桥,建成了国内首条钢桁桥梁数字化智能制造示范线,包括板材智能下料生产线、桥面板单元智能制造生产线、钢桁梁板单元智能制造生产线、钢桁梁箱型杆件智能制造生产线、钢桁梁工型杆件自动化生产线等多条自动化及智能制造生产线。通过应用数字化管理技术及智能化制造设备,在企业经营、管理、生产等各环节实现数字化、智能化与桥梁产业的深度融合。当前,钢桁桥梁制造的综合焊接自动化率由50%提升至93%。
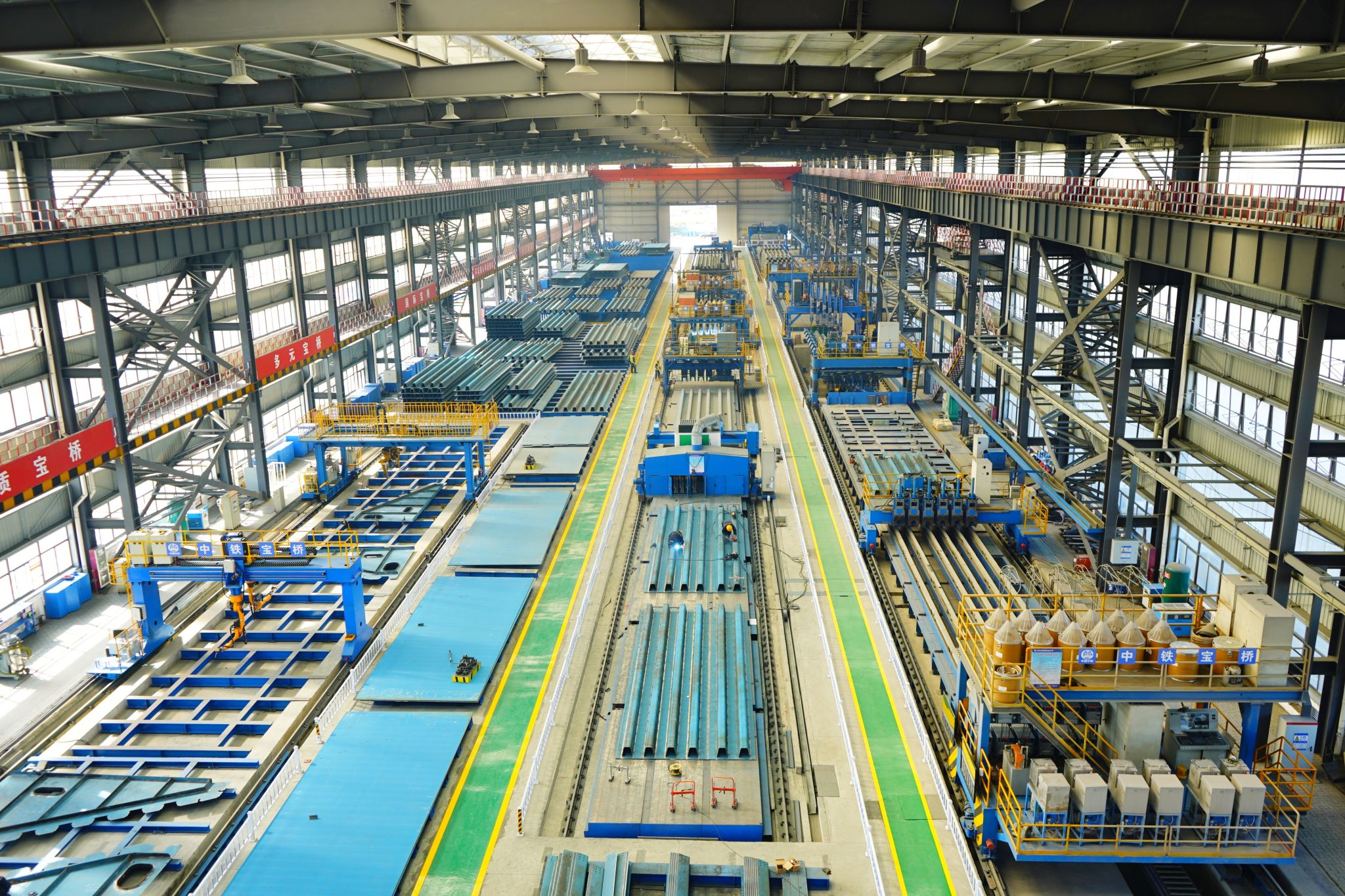
▲智能设备生产群
为提升U肋制造和焊接质量,实现常泰长江大桥8毫米U肋板单面焊缝熔透深度不低于80%U肋板厚的高精度加工要求,即将8毫米的U肋板焊透6.4毫米,如同在指甲盖上刻字,稍有闪失就有熔透的风险。中铁宝桥在原有生产线的基础上,与设备厂商联合研发包括U肋激光清洗、面板自动打磨、U肋定位组装、U肋机器人打底、U肋船外焊等设备的一整台生产线,保证焊接深度稳定一致。
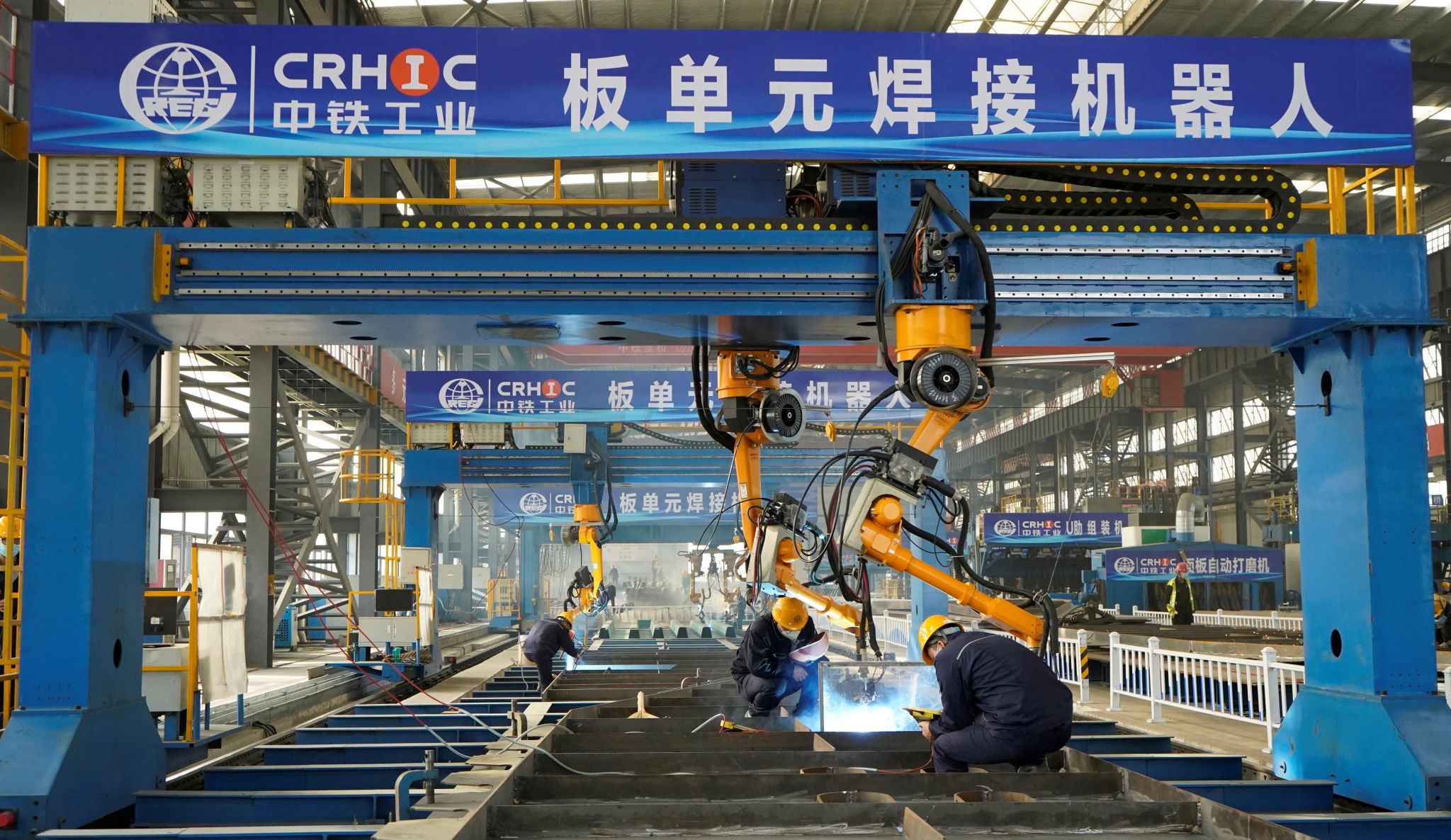
▲智能焊接机器人
此外,中铁宝桥还首次采用“成品破坏性试验+试板同步焊接+实验室检测”的工艺控制法代替传统的检测法,从成品板单元中随机抽取检测件进行破坏后的熔深监测,确保设备工艺能够达到合格标准后,生产线产品试板同步焊接,再将试板送入实验室检测,为保证U肋加工质量加上“双保险”。最终,成功实现了U肋制造工艺精细化控制,完美保证U肋80%熔深精确可控,探伤合格率达到了100%。
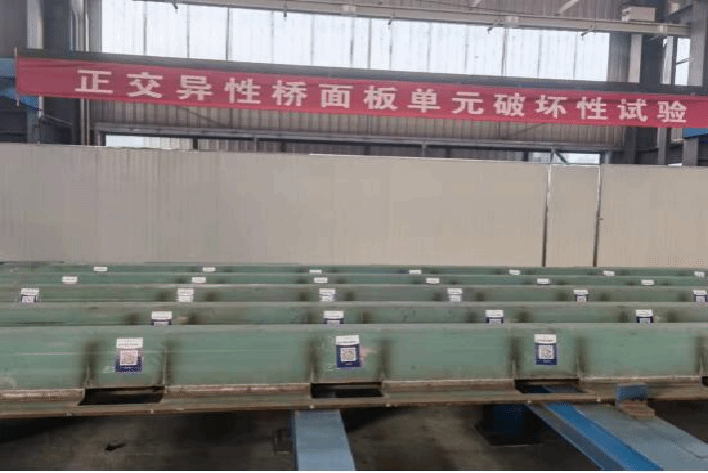
▲板单元破坏性实验
为保证常泰长江大桥的整体线形,从桁片和桥面板块到节段均采用“3+1”连续匹配制造,并且首次采用大节段“拼二焊一”工艺、工地栓接接口无应力匹配工艺、匹配孔群三维扫描技术等技术,最终保证了桥梁的整体线形。
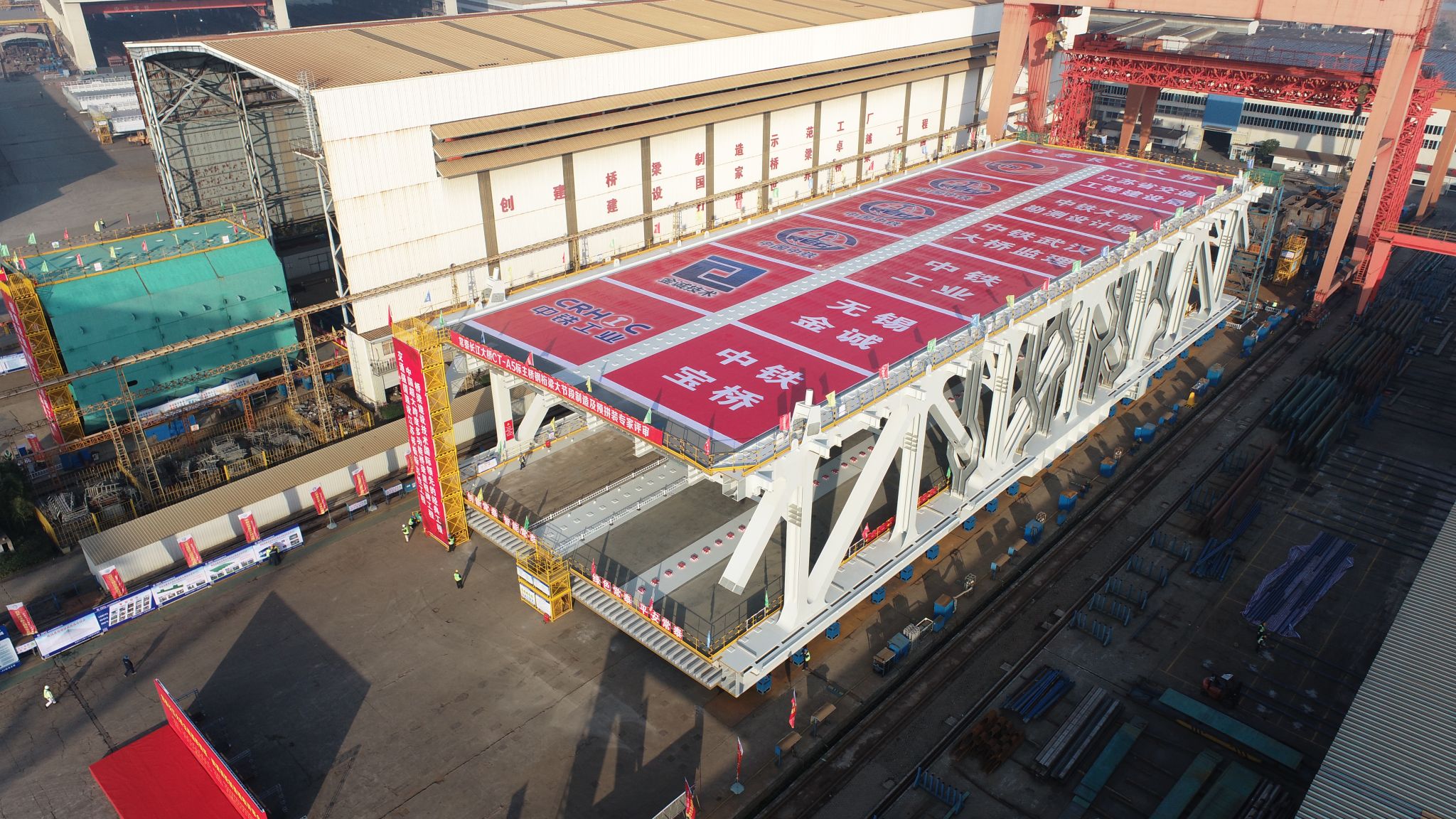
▲大节段“3+1”连续匹配制造
同时,为保证厂内制造和桥位架设的有效衔接,中铁宝桥首次采用四点支撑三维扫描测量技术,并成功进行了桥位模拟架设,实现了实体预拼加虚拟预拼双重保证。
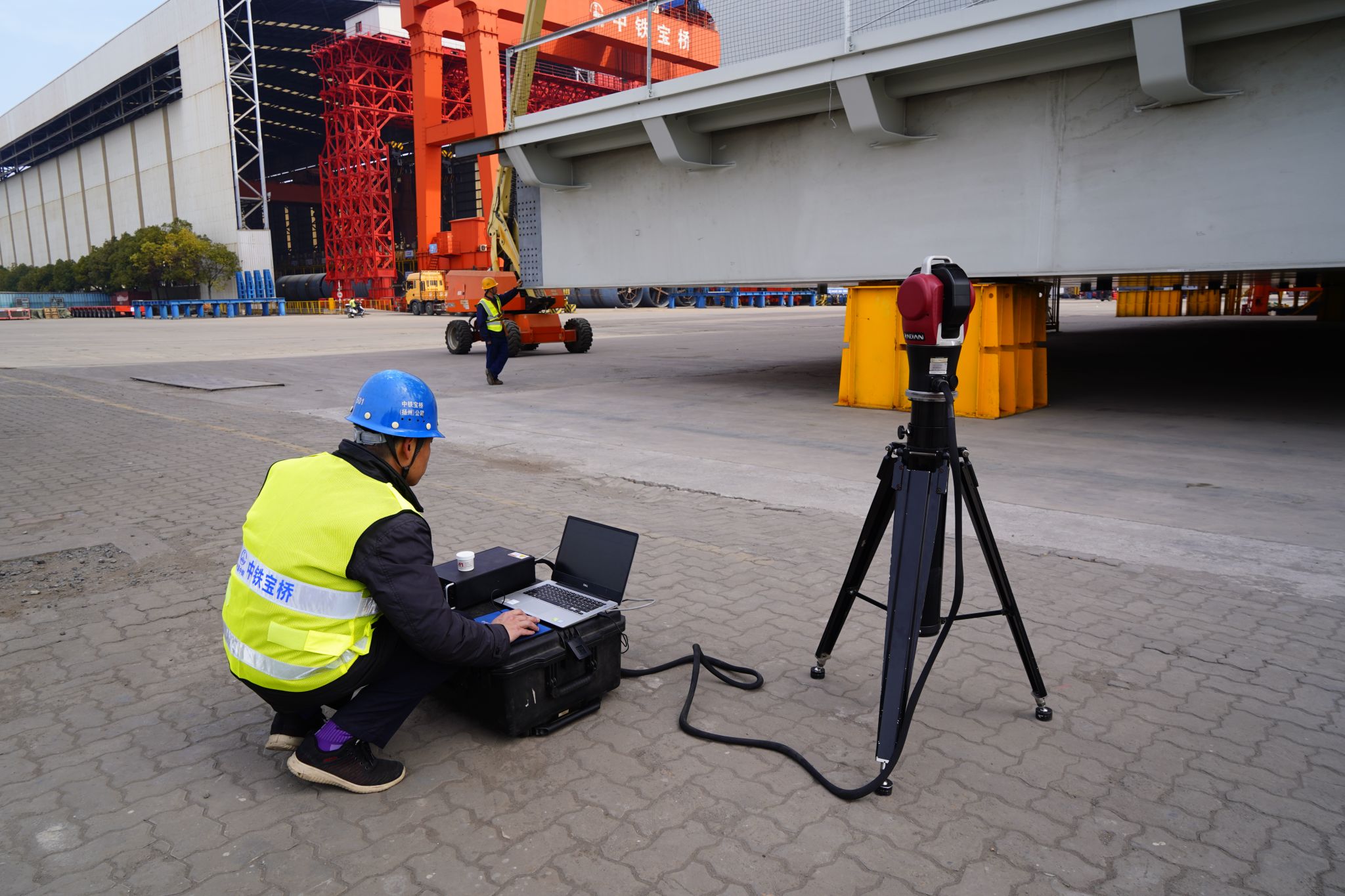
▲三维扫描设备